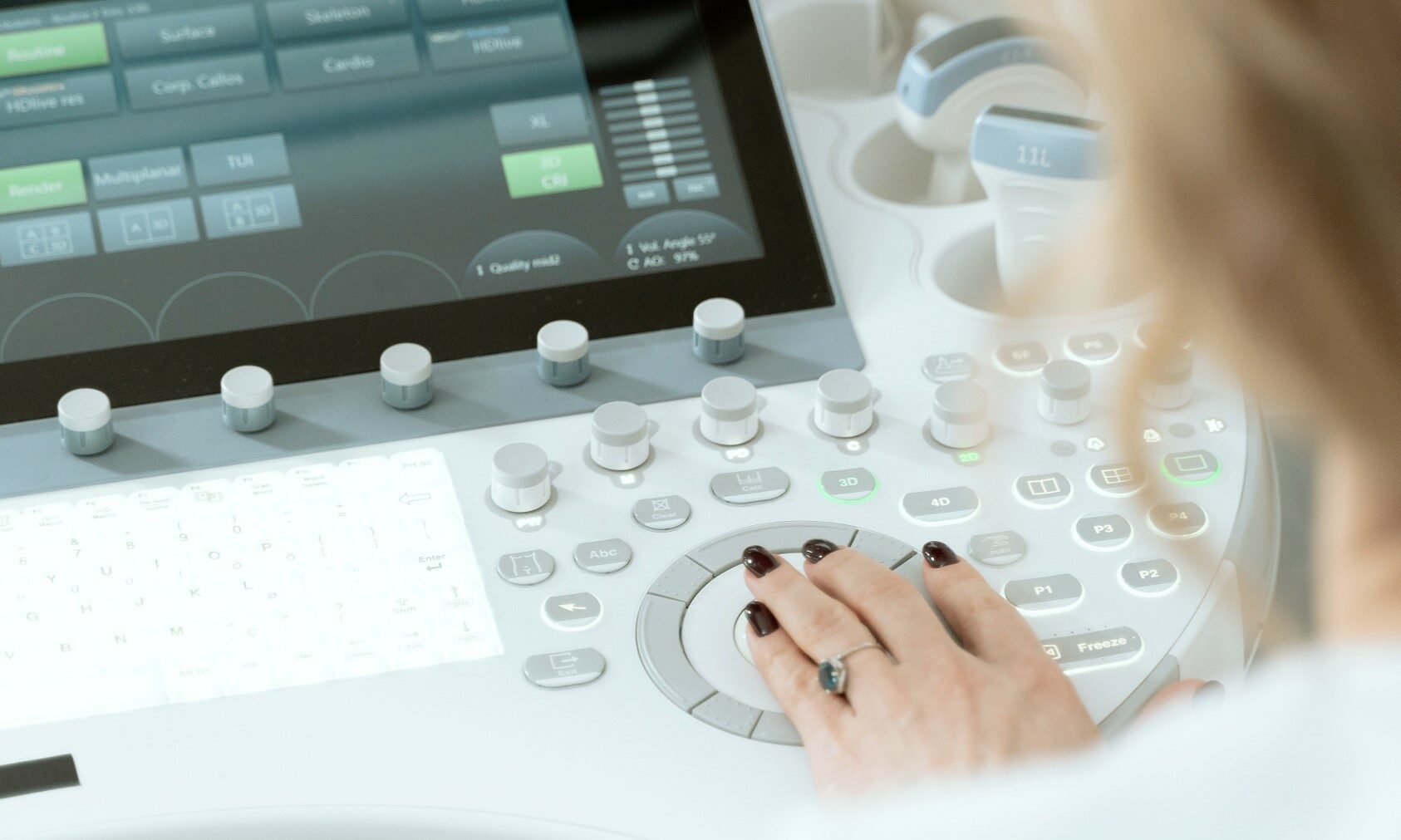
What is IEC 60601-1?
IEC 60601 is a series of safety standards examining the safety and performance of medical electrical equipment. IEC 60601-1 is the general standard of the series: it includes the basic safety and essential performance requirements for medical electrical equipment and serves to ensure that the equipment is safe under normal and single-fault conditions. ‘Single-fault safe’ is the philosophy of the standard, meaning that no single electrical, physical, thermal, or functional failure poses an unacceptable risk to people or property.
Compliance with IEC 60601-1
Many public health authorities across the globe recognise IEC 60601-1 as a prerequisite for the commercialisation of electrical medical equipment. In countries with this requirement, all electrical medical equipment must withstand the physical testing detailed in the standard (including electrical, mechanical, and temperature testing) in addition to meeting the markings, documentation, usability, software, and risk management requirements. Equipment is sent to a recognised test house, or assessor, and thoroughly tested to verify that it meets these strict requirements.
IEC 60601-1 Requirements for Sterilization, Cleaning, and Disinfection
One section of the standard tends to cause a lot of confusion and frustration. The first few clauses of section 11.6 address whether a piece of equipment can withstand spills and leaks, but the clauses that tend to lead to non-compliance require that devices are compatible with the cleaning, disinfection, and sterilisation techniques outlined in the manufacturer’s instructions for use (IFU).
During the risk management process, manufacturers must include documentation that addresses the effects of multiple cleaning/disinfection/sterilisation processes over the expected service life of their device. While 11.6.6 states that manufacturers can outline their own cleaning and disinfection procedures, 11.6.7 lists specific ISO standards for devices that require sterilisation (ISO 11135-1, ISO 11137-1, or ISO 17665-1). In either cause, many devices have not been sufficiently tested before being sent to a test house. This can lead to multiple areas of non-compliance: firstly, because the manufacturer has not provided enough evidence to support their claim of compatibility with the chosen processes, and secondly because the machine is damaged during testing when the test house follows the manufacturer’s IFU.
Compatibility testing is therefore vital, as it not only gives manufacturers a more accurate idea of the service life of their product but also provides data that can be used to prove that the product is compatible with the chosen IFU.
What happens after the testing?
There are two possible outcomes of testing:
- Equipment withstood the testing and met all the applicable requirements: the equipment is compliant.
- Equipment failed one or more tests (physical or other): the equipment is not compliant.
In either case, the test house will provide the manufacturer of the equipment with an official test report using a valid IECEE Test Report Form template.
In case of failure
Non-compliance can occur in many ways. For example:
- Failure of electrical insulation, mechanical strength, or excessive temperature.
- Failure of the legibility of marking.
- Missing information in the markings, user manual, risk management, usability, or software documents.
If the equipment is not compliant, the manufacturer can address the failures listed in the official test report and resubmit the equipment for testing. In some cases, the equipment may even need to undergo an expensive re-design process. The amount of re-work depends on a few factors:
- The nature and number of failures
- The complexity of the design
- Whether re-design is needed
Unfortunately, it is rare to have medical electrical equipment pass IEC 60601-1 testing on the first try. Depending on the above factors, re-work and re-testing can be resource- and time-intensive.
What is pre-compliance testing?
Pre-compliance testing is a valuable tool for product development, as it allows you to proactively identify potential sources of failure and address them before submitting your product for official compliance testing. A comprehensive pre-compliance evaluation covers major physical testing such as power input and temperature measurements, electrical insulation, leakage current, and dielectric strength. It also includes constructional evaluation, critical component testing, and a thorough review of product documentation. By detecting potential non-compliance ahead of time, an evaluation can save resources and time for medical devices manufacturers. For example:
- Detecting major non-compliances at the early stages of the design.
- Addressing non-compliances prior to submitting equipment to the test house.
- Avoiding re-designs and re-testing.
- Avoiding common pitfalls of IEC 60601-1 compliance testing.
- Avoiding delays in a product’s conformity assessment needs.
- Minimizing the probability of equipment compliance testing failures.
- Avoiding re-work of the accompanying documents (including re-translation of IFU).
- Avoiding re-work of markings.
- Ensuring correct ratings, classification, and types of applied parts (power rating, ingress protection, electrical class, etc).
When to seek for pre-compliance evaluation
Manufacturers can benefit from a pre-compliance evaluation at every stage of their design and development, from the early stages to the advanced. The evaluation can be customized depending on the design stage, the nature of the equipment, and its design complexity. In many cases, it is better to seek evaluation early on in the process to ensure that the requirements of IEC 60601-1 are incorporated into the product’s design requirements, making compliance to the standard far more likely.