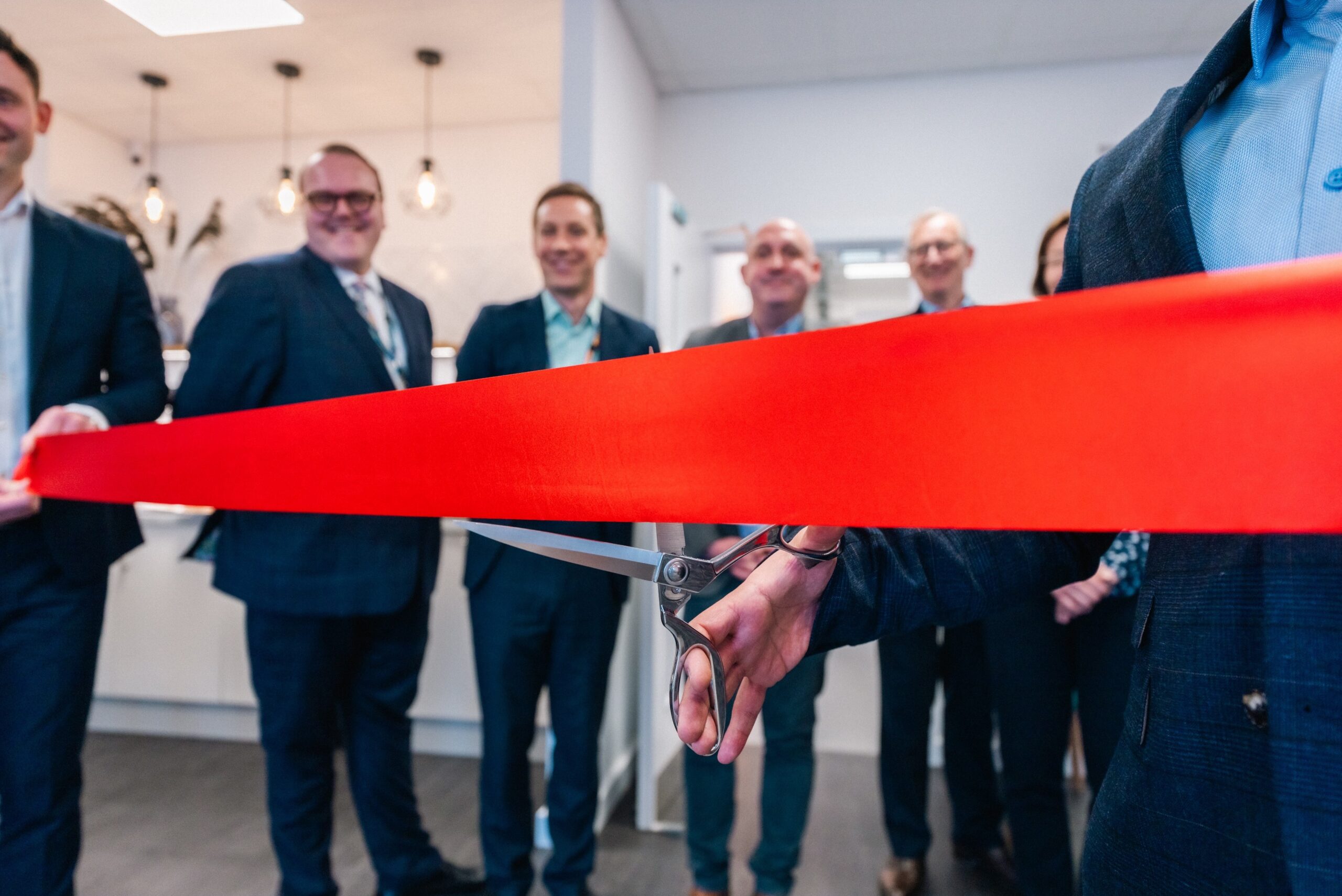
Test Labs Expands Operational Capacity with £250,000 investment in New Laboratory Facilities
On April 12, 2024, Test Labs unveiled its latest expansion initiative with the official opening of new laboratory facilities, marking a significant milestone in the company’s growth trajectory. This expansion, which entailed an investment exceeding £250,000 in state-of-the-art equipment and additional space, was made possible through securing a grant from local combined authorities.
The decision to expand comes in direct response to the surging demand for medical device testing services, underscoring Test Labs’ proactive approach to addressing the evolving needs of its customers. By boosting its operational capacity, Test Labs is poised to meet the increasing demands of the market while upholding its commitment to excellence in service delivery.
Enhancing Global Capacity in Medical Device Testing
Test Labs UK, a leading player in the medical device testing sector based in Peterborough, recently inaugurated its new facilities. The momentous occasion was marked by the presence of dignitaries from the local NHS trust, Cambridgeshire Peterborough Combined Authority, and members of the local community.
During the unveiling, guests were given a tour of the newly established laboratory facilities, guided by Enrico Allegra, the Head of Laboratory. This provided attendees with a first-hand look at the medical device testing procedures and an opportunity to engage with the scientific team.
This substantial investment has empowered Test Labs to expand its laboratory, bolstering both its capacity and capabilities. With a focus on meeting the burgeoning demand for medical device testing services, Test Labs now offers a comprehensive suite of tailored testing solutions, supported by cutting-edge specialist equipment.
Test Labs’ Managing Director, Tautvydas Karitonas, said:
“This is great news for the industry as it signals our strong response to the current medical device market challenges”
The expansion of services comes at a crucial juncture, as the demand for such testing has surpassed available capacity, both regionally and globally. This development holds promising implications for the industry and local communities alike. Test Labs’ collaboration with Peterborough University underscores its commitment to fostering educational and professional opportunities, thereby enriching the city’s talent pool and securing a brighter future for its graduates. The establishment of Test Labs’ medical device laboratory has also paved the way for the creation of highly skilled job opportunities, spanning disciplines such as biomedical engineering, microbiology, chemistry, and toxicology.
Current Medical Device Industry Challenges
Medical Device Manufacturers Technical files are missing service life validation data.
A significant number of manufacturers facing challenges due to inadequate or absent service life validation data in connection with their Instructions for Use. Typically, manufacturers establish their product service life based on factors such as the longevity of specific components or other parameters. However, the landscape is shifting, and regulatory bodies, grappling with an increasing number of field safety notices, are now scrutinising products that prematurely fail due to cleaning and disinfection practices.
Manufacturers are now expected to validate their product service life based on the real-world usage of their products, encompassing cleaning, disinfection, and sterilisation practices. This entails conducting studies to demonstrate how their products perform when reprocessed a number of times, representative of their service life. Additionally, this aligns with the requirement for basic electrical safety and essential performance tests to be completed on a reprocessed (aged) device.
Test Labs’ Business Development Manager, Marianne Browning, said:
Our clients are seeing an increase in Notified Bodies pushing back on a lack of biological evaluation plan documentation within their technical file
Manufacturers fail to provide biocompatibility data for used devices, based on their IFU reprocessing instructions
In a recent paradigm shift, manufacturers are experiencing increased scrutiny in the assessment of their biological evaluation reports and biocompatibility test reports. As part of assessing the General Safety and Performance requirements of a Medical Device, a biological evaluation is conducted to ensure that the device is safe for use and therefore does not pose a biological risk to the end user. All devices in contact with the patient must undergo biological safety assessment, or Biocompatibility. Devices will require verification regarding their performance and safety after the recommended number of reprocessing cycles. This is to further demonstrate that the repeated use of the reusable medical devices does not change or alter any physical properties which in turn may affect the biological safety of the device.
Test Labs has proactively addressed these challenges by developing and offering relevant testing services to generate the data required to satisfy regulatory bodies and bolster manufacturers’ compliance efforts.
The newly opened facilities serve as a testament to Test Labs’ dedication to continuous improvement and innovation within the medical device testing industry. With expanded capacity, the company is poised to cater to a broader range of client requirements while maintaining its reputation for excellence and reliability.