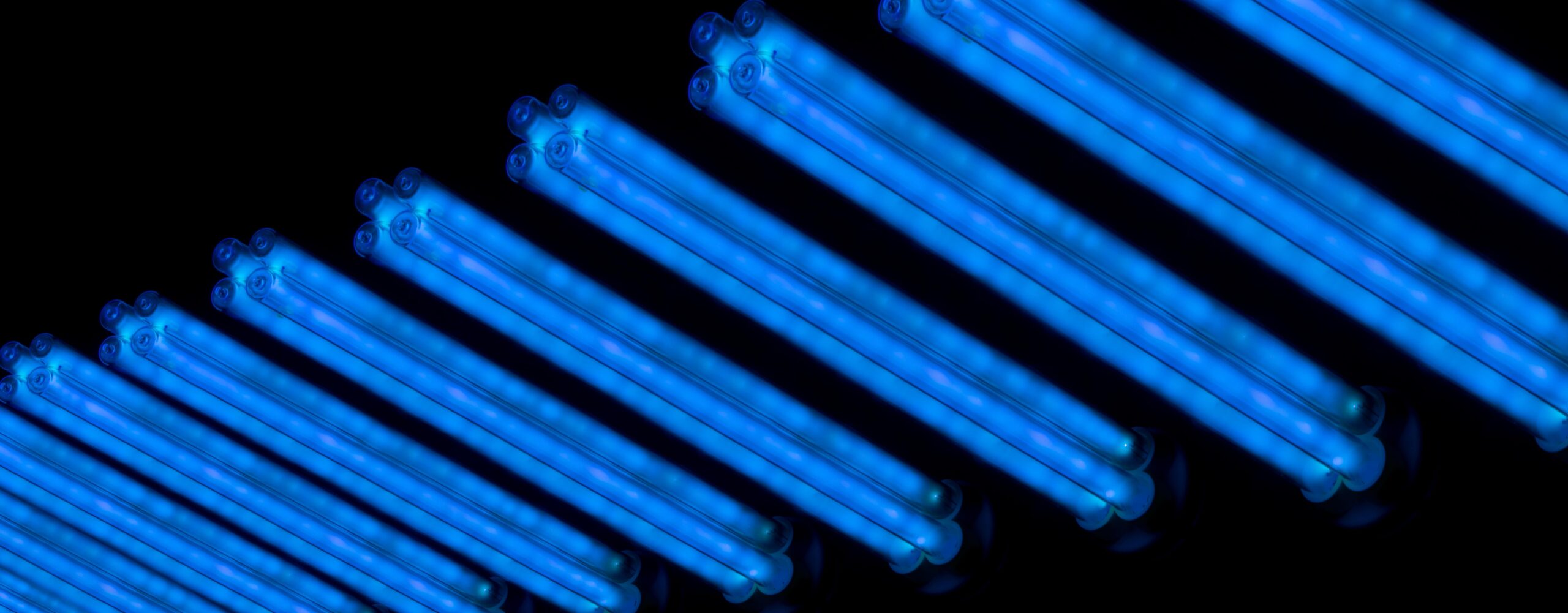
Ultraviolet (UV) irradiation has been known for decades as a terminal disinfection method, widely used in a variety of applications including healthcare, agriculture, water and food treatment, as well as in airlines and many other settings. Due to the rapid nature of the decontamination (normally between as little as 5 minutes to 45 minutes), UV devices have been implemented within healthcare settings as a quicker alternative or to complement fogging automated systems such as hydrogen peroxide dispersion technology.
UV disinfection has been shown to be a good complementation to the current manual cleaning practices, to help further reduce the risk of surface contamination. In terms of regulation, there has been a lack of standardised methodology to test UV devices in a comparable manner. For that reason, the European disinfectant standard writing body CEN has released a new standard that covers the requirements and methodology for testing the efficacy of UV devices: the BS 8628:2022.
This new standard has been based on the existing airborne surface disinfection standard EN 17272:2020 with some minor differences specific to UV devices. In brief, the UV device is placed within a blacked-out enclosed test chamber at a specified distance and location and switched on for a specified contact time. The process will be started remotely (no people present inside the chamber) and it will disinfect the surfaces and not the air in the room. Results are expressed in a logarithm scale to assess compliance with the standard.
What is the difference between the BS 8628 test and the EN 17272:2020 test?
The main difference the BS 8628 test and the EN 17272:2020 test is that the method only consists of one main phase, the Efficacy Test. The distribution test is not performed as UV devices are not intended to decontaminate the whole room but rather “close by” surfaces.
Efficacy Test of BS 8628:2022
How does the BS 8628 test work?
Stainless steel carriers are inoculated with a suspension of microorganism and interfering substance (replicating clean or dirty conditions) in triplicate per each organism and left to dry. Two control carriers are prepared similarly and will be left outside the test chamber with similar environmental conditions.
Once dry, they will be moved inside the chamber and placed horizontally over a flat black matt surface at a specified height with the inoculum facing up.
The UV system is then placed within the test chamber at specified distances from the challenge and the disinfection cycle is started.
The chamber must be equilibrated for temperature (as standard 20 ± 1 °C) and relative humidity (30-60%) before starting the cycle.
The total UV disinfection contact time is recorded, starting from the moment the UV lamps switch on to the point where they are switched off.
The carriers are then processed in a recovery liquid and plated out onto appropriate agar plates. The results are then counted, and the achieved efficacy is expressed in LOG reduction.
Our disinfectant product testing offering includes the BS 8628: Disinfection using ultraviolet radiation – Methods for quantitative testing of automated ultraviolet disinfection activities by direct illumination test standard.